The Evolution of Conveyor Rollers: How They Transformed Manufacturing
Manufacturing has come a long way since the early days of human-powered production. One crucial piece of technology that has played a significant role in this evolution is the conveyor roller.
These simple cylindrical devices have revolutionized the way factories and warehouses operate, greatly improving efficiency and productivity.
From the first rudimentary wooden rollers to the high-tech, precision-engineered rollers of today, conveyor rollers have undergone a remarkable transformation over the years.
Let’s take a closer look at the evolution of conveyor rollers, from their humble beginnings to their current state-of-the-art designs, and explore how they have transformed manufacturing as we know it.
So buckle up and get ready to discover the fascinating history of these unassuming yet highly influential components of modern industry.
The history of conveyor rollers
The concept of the conveyor belt dates back to the late 18th century when it was used to move grain short distances.
However, it wasn’t until the early 20th century that the first conveyor rollers were developed. These early rollers were made from wood and were used primarily in sawmills and other wood processing plants.
In the 1930s, metal rollers were introduced, which were much more durable and could handle heavier loads.
This led to the widespread adoption of conveyor systems in manufacturing plants, allowing for greater efficiency and productivity.
In the following decades, conveyor rollers continued to evolve, with improvements in materials, design, and technology.
The impact of conveyor rollers on manufacturing
The impact of conveyor rollers on manufacturing has been enormous. Before the widespread adoption of conveyor systems, manufacturing was a much slower and more labor-intensive process.
Workers would have to manually move materials and products from one area to another, which was not only time-consuming but also physically demanding.
Conveyor systems, powered by rollers, changed all that. They allowed for the automated movement of materials and products, greatly reducing the need for manual labour.
This not only made manufacturing faster and more efficient but also safer for workers, who were no longer required to perform back-breaking tasks.

The different types of conveyor rollers and their uses
There are several different types of conveyor rollers, each with its own unique characteristics and uses. Gravity rollers, for example, rely on the force of gravity to move products along the conveyor system.
These are commonly used in warehouses and distribution centers for the movement of large, heavy items.
Motor-driven rollers, on the other hand, are powered by an electric motor and are used in more complex conveyor systems. These rollers can be programmed to start and stop automatically, allowing for greater control over the movement of products and materials.
Other types of conveyor rollers include tapered rollers, which are used to help guide products along the conveyor system, and sprocket-driven rollers, which are commonly used in food processing plants to move delicate items such as baked goods.
Modern advancements in conveyor roller technology
Conveyor roller technology has come a long way since the early wooden rollers of the 20th century. Today’s rollers are made from a variety of materials, including steel, aluminum, and plastic, which offer greater durability and longevity.
Modern conveyor rollers also feature precision-engineered bearings and seals, which help to reduce friction and wear, prolonging the life of the roller. In addition, many modern rollers are designed to be easily replaceable, allowing for quick and efficient maintenance.
One of the most significant advancements in conveyor roller technology in recent years has been the integration of sensors and other high-tech devices.
These sensors can be used to monitor the movement of products and materials, ensuring that they are moving smoothly and efficiently through the system. They can also be used to detect and alert workers to potential problems, such as jams or blockages.
Common issues with conveyor rollers and how to fix them
Like any piece of machinery, conveyor rollers can experience problems from time to time. Some of the most common issues include roller misalignment, roller seizure, and roller damage.
Roller misalignment can occur when the rollers become skewed or tilted, causing products to move off the conveyor belt. This can be fixed by adjusting the alignment of the rollers or replacing damaged rollers.
Roller seizure occurs when the rollers become stuck or jammed, preventing the movement of products along the conveyor system.
This can be caused by a variety of factors, including dirt and debris, worn bearings, or damaged rollers. To fix this issue, workers must identify the cause of the seizure and remove any debris or replace any damaged components.
Roller damage can occur over time due to wear and tear or as a result of accidents or collisions. Damaged rollers can cause products to move unevenly or become stuck in the system, leading to delays and inefficiencies. To fix this issue, damaged rollers must be replaced with new, undamaged ones.
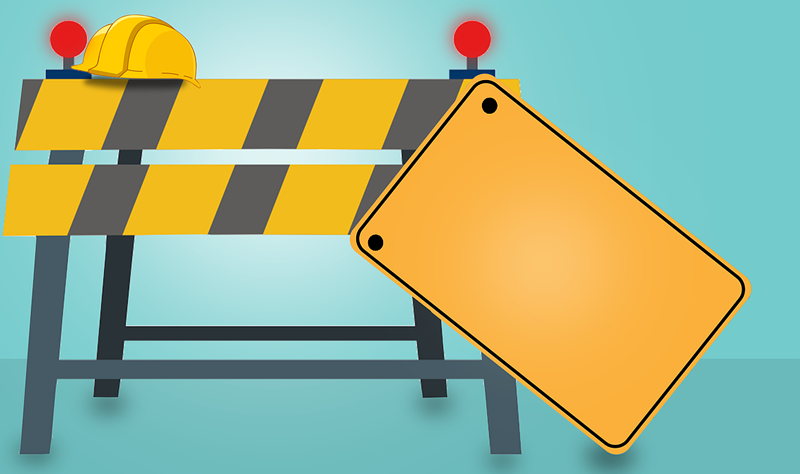
Safety considerations when working with conveyor rollers
Working with conveyor rollers can be dangerous if proper safety precautions are not taken.
Workers must be trained on the safe operation and maintenance of conveyor systems, and must always wear appropriate personal protective equipment, such as gloves and safety glasses.
In addition, workers must be aware of the potential hazards associated with conveyor systems, such as pinch points, entanglement hazards, and falling objects. They must also be trained on emergency procedures in case of accidents or malfunctions.
Regular maintenance and inspection of conveyor systems are also critical to ensuring worker safety. Workers must be trained to identify potential safety hazards, such as damaged rollers or misaligned belts, and to report them immediately to their supervisors.
Future developments in conveyor roller technology
The future of conveyor roller technology looks bright, with continued advancements in materials, design, and technology.
One area of particular interest is the use of robotics and automation in conveyor systems, which could greatly improve efficiency and productivity.
Other areas of focus include the development of more eco-friendly materials and systems, as well as the integration of artificial intelligence and machine learning into conveyor systems.
These technologies could help to reduce waste, improve energy efficiency, and make conveyor systems even more intelligent and responsive.
Case studies of successful conveyor roller implementation
There are countless examples of successful implementation of conveyor rollers in manufacturing and other industries.
For example, in the automotive industry, conveyor systems are used to move car parts along the assembly line, greatly reducing the need for manual labor.
In the food processing industry, conveyor systems are used to move delicate items such as baked goods and pastries along the production line, ensuring that they are handled with care and precision.
In the logistics industry, conveyor systems are used to move packages and parcels along the distribution center, allowing for faster and more efficient processing and delivery.
Conclusion: The future of conveyor rollers in manufacturing
Conveyor rollers have come a long way since their humble beginnings in the early 20th century. Today’s rollers are high-tech, precision-engineered components that have transformed manufacturing and other industries.
As technology continues to evolve, so too will conveyor roller technology, with continued advancements in materials, design, and automation.
The future of conveyor rollers in manufacturing looks bright, with endless possibilities for improving efficiency, productivity, and worker safety.