The Different Types of Conveyor Rollers and Their Uses
Conveyor rollers are a key component of any efficient conveyor system, and there are a variety of different types that can be used to meet the needs of different applications and industries.
They are designed to reduce the friction between the roller surface and the belt, enabling materials to move more smoothly along the line. Each type of roller offers its own unique set of benefits and depending on the specific needs of a conveyor system, one type may be more suitable than another.
So let’s take a look at the different types of conveyor rollers and their uses, so you can make an informed decision when designing or purchasing a conveyor system.
What are conveyor rollers?
Conveyor rollers are the components used to transfer the motion of the drive wheels to the moving chains or belts of a conveyor system.
They are composed of a hard, durable material such as metal, including cast iron, steel, stainless steel, or aluminum, and are coated with a softer material, such as rubber, synthetic rubber, or urethane, to reduce friction with the moving belt.
Conveyor rollers are cylindrical in shape, with a smooth surface designed to minimize the buildup of dust and other materials. They are typically installed vertically on a roller track, with drive wheels or sprockets at the top and a chain or belt running along the bottom.
The rollers themselves are continuously rotating, while the belt moves at a slower pace. Conveyor rollers are also referred to as drive wheels, drive pulleys, or drive roller assemblies.

Types of conveyor rollers
There are a variety of different types of conveyor rollers on the market today, each with its own set of benefits and uses.
As you’re selecting the best roller for your application, it’s important to consider not only the type of roller, but also the length and diameter. The diameter of the roller is one of the biggest factors in determining the capacity of the roller – the heavier the load, the larger the diameter you’ll need.
The length of the roller also plays a role in determining the capacity, but it also affects the amount of sag in the conveyor belt or chain at the roller.
Here are some of the most common types of conveyor rollers:
- Back-tension rollers – These rollers are designed with a slight backward tension on the chain or belt, which helps to hold the chain or belt in place. They are often used in cold storage facilities, where temperatures are consistently kept low, as these types of roller are less susceptible to freezing and becoming stuck due to moisture.
- Direct-drive rollers – These rollers are used to transfer motion from the drive wheel to the moving chain or belt through a roller that is mounted directly on the shaft of the drive wheel.
This type of roller is typically used on shorter conveyor systems, due to the higher load capacity of the drive wheel.
- Drive idler rollers – As the name suggests, this type of roller is used as an idler for the moving chain or belt and is mounted between the drive wheel and the chain or belt. They are often used in industrial environments where long spans of conveyor belts are required, as they allow for longer spans of belts compared to direct-drive and back-tension types of rollers.
- Drive sprockets – Sprockets are often used to provide drive to slower-moving belts or chains and can be either direct-drive or idler-style rollers.
Benefits of different types of conveyor rollers
As we’ve discussed, each type of roller has its own unique set of benefits. These benefits are what make certain roller types more suitable for certain conveyor applications than others.
For example, back-tension rollers are designed with a slight backward tension on the chain, which helps to keep the chain in place, even in environments where there is a lot of dust or dirt.
Similarly, drive sprockets are often used to provide drive to slower-moving belts or chains, and provide a slower speed than direct-drive and back-tend roller types.
When selecting the best roller type for your application, it’s important to keep these benefits in mind, so the roller can best serve its purpose, and the conveyor system as a whole can be as efficient and effective as possible.
Common applications for conveyor rollers
Conveyor rollers are used in a variety of industries, including cold storage and food processing plants, manufacturing plants, warehouses and transportation systems.
Some of the most common applications include:
Cold storage – Cold storage warehouses often rely on conveyor systems to move pallets of perishable goods, such as fruits and vegetables, from the receiving dock to the storage aisles.
This type of conveyor system often utilizes overhead trolleys, with hooks at the end to move the pallets from the receiving dock, and roller conveyors at the tops of the storage aisles to move the pallets from one aisle to the next.
Food processing – Food processing plants also often use conveyors to transport materials from one station to the next. Roller conveyors are ideal for this application because they are easy to clean and can be used to move almost any type of product, regardless of size or weight.
Manufacturing – Roller conveyors are used in many industries, but especially in manufacturing plants, where they are used to transport materials throughout the plant, such as parts, products, and raw materials.
Warehousing – Roller conveyor systems are used in warehouses to transport goods from the receiving dock to the shipping area.
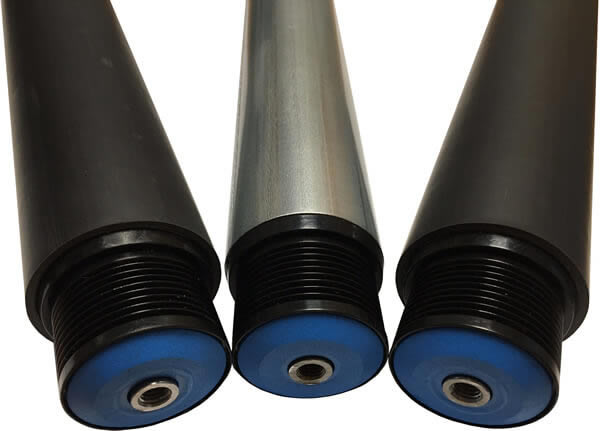
Factors to consider when choosing conveyor rollers
There are a number of factors to consider when selecting the best roller for your application. To make sure you’re selecting the right type of roller for your needs, it’s important to take the following factors into account:
- The length of the roller – When selecting a length for your roller, it’s important to take into account the weight of the load being moved. Longer rollers will result in more sag in the belt or chain, which can cause issues with load adjustment.
- The diameter of the roller – The larger the diameter of the roller, the greater the capacity of the roller. A heavier load will require a larger diameter roller.
- The type of roller – Each type of roller has its own unique set of benefits, so it’s important to select the type of roller that best meets the needs of your conveyor system.
Tips for maintaining and caring for your conveyor rollers
As with any other mechanical component of your manufacturing or warehousing operation, proper maintenance is key to ensuring the longevity of your conveyor rollers.
The following tips can help you care for your rollers to ensure they last as long as possible:
Inspect the roller regularly for any signs of damage, such as cracks or broken parts. If you notice any issues, have the roller serviced or replaced as soon as possible.
Clean your roller regularly to remove dirt, grime, and other debris that can build up and cause damage.
Clean your roller after every use if it is used in a dusty environment.
How to choose the right conveyor roller for your application
When selecting the best roller type for your application, it’s important to consider not only the type of roller, but also the length and diameter.
Here are a few steps you can follow to select the right roller type for your application:
Decide on the length of the roller – First, decide on the length of the roller. Once you know the length of the roller, you can determine the weight of the load the roller will have to support, which will help you select the correct diameter.
Select the diameter of the roller – Once you know the length of the roller, select the diameter of the roller that will be able to support the load.
Select the type of roller – Once you know the length and diameter of your roller, you can select the type of roller that will best meet the needs of your application.
Conclusion
Conveyor rollers are a key component of any efficient conveyor system, and there are a variety of different types that can be used to meet the needs of different applications and industries.
Each type of roller offers its own unique set of benefits and depending on the specific needs of a conveyor system, one type may be more suitable than another.
If in doubt, speak to AED Rollers for professional advice.